Introduction – What is Drive-By-Wire?
Developing safe connected, autonomous vehicle technology is hard and time-consuming. What’s more, interfacing an autonomous driving system with any given vehicle is a severely underpublicized industry challenge, especially when considering how to make the entire autonomous system as safe, scalable, and flexible as possible.
The system enabling this interface is known as the ‘drive-by-wire’ system. This provides the means to control the throttle, steering, braking, gears and ancillary systems of a vehicle, to enable eventual vehicle automation. Drive-by-wire (or X-by-Wire as it is sometimes known, abbreviated to DBW) means electronic replacement of traditional mechanical linkages connecting the vehicle to the driver.
In the autonomous vehicle world, the drive-by-wire system enables the autonomous software, or teleoperation software, to provide commands to the vehicle, using control methodology to steer, brake, accelerate and change gear where necessary, whilst also passing back data on the current vehicle “state”. This system, as we will uncover, can take a number of different guises, from full “robot-in-the-seat” systems to systems that simply send electronic messages (via vehicle CANBus) to existing power-assisted vehicle architecture.
Whilst much effort (and investment) has been put into autonomous software, it is the “automotive” technology stack present in the vehicle that enables the autonomous software to “drive” a vehicle. , Therefore the drive-by-wire system, and the safety analysis of that system, remains the most critical hygiene factor for autonomous vehicles, with huge implications for safety, reliability, scalability and time-to-market.
This series of blogs will uncover some of the most important considerations around drive-by-wire, introduces StreetDrone’s solution, XCU, and why we believe it to be the optimum way to test, develop and scale autonomous vehicle deployments.
We start with a buyers guide; what are the things you should look out for when considering purchasing a drive-by-wire vehicle platform, or even when considering building a DBW vehicle versus buying one?
Buyer’s Guide – What are the most important considerations when purchasing a retrofit DBW system?
- Safety
Front and centre of the drive-by-wire challenge is safety. Is the drive-by-wire system built in line with ISO 26262 standards? Does the drive-by-wire system have independent channels of sensors to detect faults? Can we ensure that we can disable the system when we need to? Is there a functional safety analysis document that comes with my drive-by-wire system? What is the method of control involved (e.g. CANBus manipulation versus adding actuators/driving robots).
These are just some of the myriad of questions that might arise when considering safety implications around drive-by-wire systems. What is sure, is that being able to rely on drive-by-wire is essential to build a wider safety case around autonomous vehicle deployments.
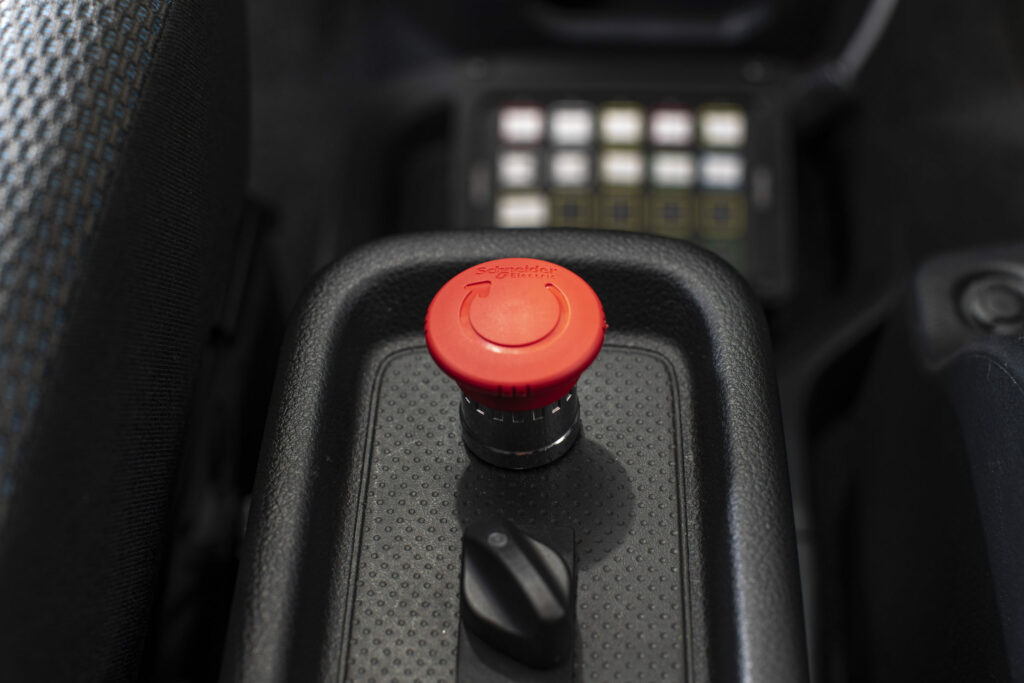
- Operating “Level”
Related to the safety pointers above, are considerations around the “level” of the drive-by-wire system. Those familiar with the SAE levels of autonomy will have some idea of the reference here which focuses on the level of maturity of autonomous technology and the presence of a “safety” driver. Most DBW systems in the market today are termed as “Level 2” and require an alert, trained safety driver to be ready to take over at all times. Some suppliers are developing Level 4 systems, where you can take the safety driver out of the loop, within certain scenarios also called Operational Design Domains, see our blog on those here.
The key thing to consider, in both circumstances, is what do I expect the vehicle to do when something goes wrong. If it’s hand control back to the safety driver, then great, level 2 is for you. If you intend to have no safety driver involved, then a much more involved conversation with the supplier is involved, with critical conversations around redundancy of actuation (e.g. backup if a steering motor fails) and minimum risk manoeuvre (e.g. getting the vehicle to pull to a safe-stop without human intervention).
- Interface
A short but important consideration – how do you intend to use the drive-by-wire system? Most systems are based on “CANBus”, the standard for on-vehicle communications, but some suppliers will provide other interfaces, such as ROS – see an example here, which act as a translator between CAN and the chosen programming language for the autonomous driving stack.
This will be a question for your autonomous vehicle R&D team!
- Usability
An important part of the drive-by-wire system, particularly when looking at R&D applications, is system usability, centred around the human-machine interface. How a safety driver can arm and initiate the system, and how that safety driver then disables the system in case of error is key to all occupants and engineers having confidence in the vehicle.
Disabling a DBW system is an important part of the wider safety considerations, with the best drive-by-wire systems offering intuitive takeover methods, such as grabbing the wheel, or pressing the brake as easy ways to disable the system if the autonomous driving software has not performed as expected. This is in addition to switches, big red buttons and other features which ensure the safety driver feels comfortable and in control of the overall system when in testing.
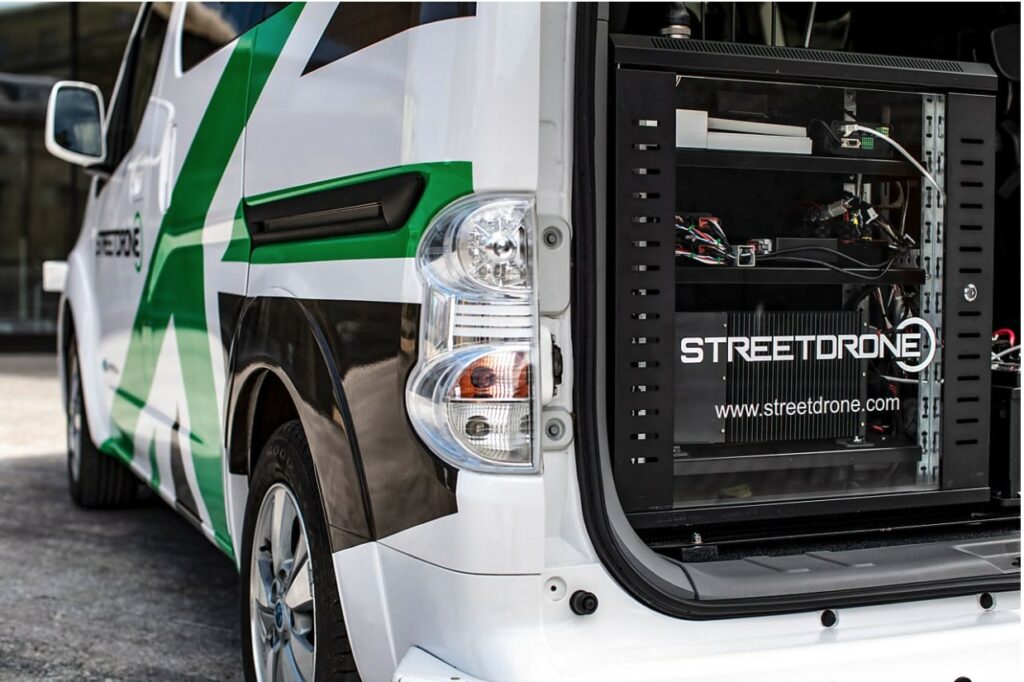
- Reliability and Support
In order to deploy autonomous vehicles on the road, developers need to be able to access test vehicles as and when they need them. A big part of this is ensuring that the system is reliable, with maximum uptime to ensure that developers can maximise their road miles.
An important part of this is having detailed documentation, maintenance schedules and dedicated support to troubleshoot integration issues, and keep the vehicle available for testing as and when required..
- Legality and Regulations
Each and every country is different when it comes to the regulation of retro-fit drive-by-wire systems, destined for public-road trials. In the UK, such systems need to comply with UK Construction and Use laws, and may be subject to Single Vehicle Approval should the modifications be deemed “radical”. Different territories take different approaches to this, with organisations such as TÜV SÜD providing licenses in countries such as Germany.
However, behind each and every deployment of a drive-by-wire vehicle for research purposes should be a solid safety analysis that can be applied to the relevant laws, regulations and approval processes for the designated country.
- Scalability
A developer may aim to be using a drive-by-wire to develop a system relevant to many vehicle types, and suitable for wider deployment, for example, an ADAS feature for mine vehicles. As such the scalability of such systems to multiple different vehicle types, across use cases and manufacturers.
Some drive-by-wire providers may be able to retrofit their drive-by-wire systems to multiple vehicles, from vans to dump trucks, ensuring the same “interface” to minimise the effort in scaling deployments.
Even when starting with one test vehicle, it should be considered how the CAV technology will ultimately end up in the field.
- Vehicle
We’ve left this one until last because it’s probably the most fun… which vehicle am I going to choose for my drive-by-wire system? Does my drive-by-wire solution allow work to commence on an “easy-to-use” test vehicle, before migrating to a use-case specific vehicle, be it a dump truck or a minibus? Does the supplier have the vehicles “off-the-shelf” or do I need to enquire with regard to a bespoke project?
We hope that these tips help you when choosing your next drive-by-wire system. To discuss your needs, and to receive advice from our expert team, please do not hesitate to get in touch.